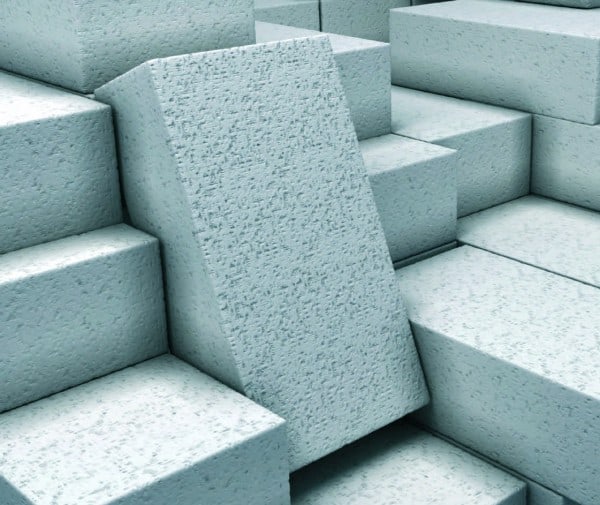
Газобетон стал популярен благодаря оптимальному сочетанию прочности, легкости, долговечности, простоты обработки, теплоизоляционных свойств и приемлемой цены. Поэтому многие застройщики используют газобетон для возведения жилых зданий малой этажности, гаражей, ангаров и других нежилых сооружений.
Технология производства газобетона не является сложной, но требует специального автоклавного оборудования. Материал, получаемый неавтоклавным способом, не соответствует государственным стандартам по ряду характеристик, а значит, не может быть использован в некоторых сферах жилого строительства. Кроме того, большое влияние на параметры и геометрию блоков оказывает выбранная рецептура производства и исходное сырье. Таким образом, потенциальному изготовителю газобетона необходимо вдумчиво изучить технологию и приобрести весь спектр необходимого оборудования.
Содержание
История изобретения
Впервые газобетон создал чешский изобретатель Гоффман в 1889 году. В структуру обычного бетона он добавил кислоты и различные соединения углерода. Понятно, что они начали взаимодействовать и производить поры. Его изобретение не осталось незамеченным, и вскоре Гоффман получил патент на свое детище. Через два десятилетия, в 1914 году газобетон Гоффмана усовершенствовали двое американских ученых, начавшие использовать в процессе производства порошки алюминия и гашенную известь. Такая технология с небольшими изменениями сохранилась и до сегодняшнего дня. Ещё через десятилетие деятельность американцев продолжил шведский архитектор Эриксон, которые несколько усовершенствовал формулу газобетона и сделал ещё дешевле. Как результат, в 1929 году в родном городе архитектора (Иксхольт) было открыто первое в мире массовое производство.
Виды газобетона
Газобетон – строительный материал в виде ячеистых блоков, изготовленных автоклавным твердением. По плотности различают газобетон:
- Теплоизоляционный (марки D300-D400). Материал легкий и наименее прочный среди всех видов газобетона, однако обладает прекрасными теплоизоляционными качествами. Показатели плотности – 300-400 кг/м³, коэффициент теплопроводности – 0.09 и выше.
- Конструкционно-теплоизоляционный г-н (марки D500-D900). Показатели плотности – 500-900 кг/м³, коэффициент теплопроводности – 0.14-0.28. Является самым популярным видом газобетона.
- Конструкционный г-н (марки D1000-D1200). Применяется для возведения сооружений, рассчитанных на существенные нагрузки. Показатели плотности газобетона – 1000-1200 кг/м³, высокий коэффициент теплопроводности.
В качестве кремнеземистой составляющей газобетона может использоваться зола, песок и прочие материалы для производства. В зависимости от этого меняется ряд показателей, например, коэффициент теплопроводности и плотность. Вяжущий компонент также зависит от рецептуры. Это могут быть известь, цемент, шлак, зола или смесь нескольких компонентов.
Категория газобетонным блокам присваивается на основании геометрических параметров. Для продукции первой категории отклонения от государственного стандарта не должны превышать 1.5 мм – по типоразмерам и 2 мм – по диагонали. Такие блоки можно укладывать на клей с минимальной толщиной шва. Отклонения для изделий второй категории составляют не более 2 мм и 4 мм, соответственно, для третьей – 4 мм и 6 мм.
В зависимости от области применения блоки газобетона бывают перегородочными и стеновыми. Первые используются для возведения ненесущих конструкций внутри зданий, вторые – для строительства наружных стен.
Что касается конфигурации и типоразмеров блоков газобетона, производство которых будет рентабельным для нового предприятия, то на первых порах можно ограничиться следующими изделиями:
- Газобетон прямоугольной формы (625 мм в длину, 250 мм в высоту, 100, 150, 200, 240, 300 или 400 мм в ширину).
- U-образной формы (600 мм в длину, 250 мм в высоту, 200, 240, 300 или 400 мм в ширину).
Прочно встав на ноги, можно подумать о расширении производства за счет изготовления под заказ газобетонных блоков нестандартного типа.
Оборудование для производства газобетона
Выбор оборудования зависит от производственных масштабов. На рынке представлен широкий спектр конвейерных, стационарных и мобильных установок от разных производителей. Каждый вариант обладает своими особенностями.
Конвейерные линии
По сути, речь здесь идет о полноценном заводе с максимальной автоматизацией процессов, большими объемами производства газобетона и, соответственно, высокой рентабельностью.
В составе линии для производства присутствуют следующие агрегаты:
- емкости и бункеры для сырьевых компонентов;
- ленточные конвейеры;
- смесители;
- автоклавы;
- формы для заливки смеси;
- установки для разрезания газобетона;
- дробильный аппарат;
- тележки;
- аппаратная часть для управления автоматическими процессами;
- вилочный погрузчик.
Стоимость комплекта оборудования может составлять от 5 до 55 миллионов рублей в зависимости от мощности и страны производства. В среднем заводы такого типа дают возможность выпускать порядка 300 тыс. м³ газобетонных блоков ежегодно и требуют для размещения площади в несколько тысяч квадратных метров.
Стационарные линии
Производительность предприятий этого типа составляет около 50 м³ газобетона в сутки. В комплектацию входят дозаторы сырья, ленточные транспортеры, автоклав и другие оборудование. Основное отличие от конвейерных линий состоит в низком уровне автоматизации, поэтому для обслуживания необходимо нанимать большее количество рабочих.
Для размещения всех агрегатов, складских площадей и бытовых помещений потребуется цех площадью порядка 500 м².
Мобильные линии
Этот вариант самый бюджетный и оптимален для предпринимателей с небольшим стартовым капиталом либо строительных фирм, желающим иметь собственное производство газобетона. В зависимости от конфигурации оборудование дает возможность изготавливать 10-30 м³ газобетона в сутки.
При этом важно понимать, что наряду с непосредственно производственной линией, предприятию по изготовлению газобетона потребуются погрузочно-разгрузочная техника и различный инвентарь. В наименьшем варианте это около 150 тыс. руб. Если же планируется приобретение грузового транспорта для доставки блоков, капитальные затраты существенно возрастают.
Технология изготовления газобетона + Видео как делают
Сырье
Будущему производителю необходимо наладить поставки портландцемента марок 300, 400, 500, параметры которого должны соответствовать ГОСТ 970-61. Также потребуются:
- кварцевый песок, зола унос ТЭЦ, маршалит или другой кремнеземистый компонент;
- чистая вода;
- известь;
- газообразующий компонент, например, алюминиевая пудра;
- специфические добавки, ускоряющие твердение газобетона и улучшающие параметры готовых блоков.
Важно проконтролировать качество сырья, поскольку наличие примесей негативно сказывается на процессе газовыделения, что чревато браком.
В целом рецептура подбирается индивидуально. При отсутствии опыта в отрасли производства газобетона желательно привлечь профессионального технолога.
Если поиск оптимальной рецептуры своими силами экономически не рентабелен или по тем или иным причинам невозможен, производство газобетона можно наладить на основе готовых смесей. Они поставляются в сухом виде, а для замешивания потребуется лишь добавить нужное количество воды.
Описание процесса
Производство блоки из газобетона проводят в строгом соответствии с ГОСТ 21520-89 «Блоки из ячеистых бетонов стеновые мелкие. Технические условия» и ГОСТ 31360-2007 «Изделия стеновые неармированные из ячеистого бетона автоклавного твердения. Технические условия».
Сам технологический цикл включает следующие этапы производства:
- Приемка и проверка характеристик сырья.
- Дозирование шлама, подогрев и предварительное смешивание. Нужное количество сырья для производства автоматически подается в ванну-дозатор, где смешивается и подогревается при помощи острого пара до 40-45° С.
- Помол и смешивание. Компоненты перемешиваются до получения смеси нужной консистенции в газобетономешалке пропеллерного типа.
- Формирование будущих блоков. Посредством резинотканевых рукавов состав заливается в формы, предварительно смазанные минеральным маслом, что необходимо для облегчения выемки блоков из форм.
- Вспучивание, схватывание и твердение. Важное условие – температура в цехе не должна опускаться ниже +25° С. В ходе вспучивания у газобетона образуется «горбушка», которая затем срезается механическим либо ручным инструментом.
- Резка блоков. Затвердевшая масса извлекается из форм и нарезается на блоки установленного размера.
- Автоклавирование. Блоки помещаются на вагонетки в 2-3 яруса и подаются в автоклав, где приобретают установленные стандартами параметры.
- Приемо-сдаточный контроль. Каждая партия изделий проходит приемо-сдаточные испытания. В ходе них определяются соответствие размеров, прямолинейности ребер, разности длин диагоналей, глубины отбитости углов и ребер, средней плотности, прочности на сжатие установленным стандартам. Всё это фиксируется в сопроводительной документации. Порядок проведения испытаний регулируется ГОСТ 31360-2007.
- Упаковка и хранение. Готовые газобетонные блоки укладываются в штабели и фиксируются термоусадочной пленкой либо другим способом, обеспечивающим отсутствие повреждений. Поскольку газобетон является гигроскопичным материалом, хранить его необходимо на поддонах в условиях, обеспечивающих защиту от действия влаги.
Существует два способа производства газобетона: мокрый и сухой. С экономической точки зрения первый является более выгодным. В этом случае кремнеземистый компонент с известью перемалывается в присутствии подогретой воды с выделением шлама. Сухой способ производства предусматривает помол и смешивание при помощи шаровых мельниц. Далее шлам поступает на сито для удаления крупных фракций, оттуда – в сборник, а затем – в шламовый бассейн, где подвергается непрерывному помешиванию и барботажу.
Видео:
Сопроводительная документация на продукцию
В соответствии с ГОСТ 31360-2007, реализация каждой партии газобетонных блоков должна сопровождаться документом, удостоверяющим качество продукции. В нем указывают:
- наименование и адрес компании-производителя;
- назначение газобетонных блоков;
- условное обозначение продукции;
- объем партии;
- типоразмеры блоков;
- марку по средней плотности;
- класс по прочности на сжатие;
- удельную эффективную активность естественных радионуклидов;
- коэффициент теплопроводности в сухом состоянии;
- коэффициент паропроницаемости;
- дату выдачи документа, его номер;
- указание на действующий стандарт.
При этом клиент имеет право на проведение испытаний в независимой лаборатории для подтверждения качества блоков.
Рентабельность бизнеса
Размер прибыли конкретного предприятия зависит от объемов производства и реализации, цен на газобетон в регионе реализации и типа выпускаемого продукта. Для расчета капиталовложений предпринимателю необходимо учесть следующие пункты расходов:
- регистрация деятельности, оформление документов;
- приобретение оборудования и пусконаладочные работы;
- закупка сырья для производства минимум на два месяца работы;
- строительство или ремонт производственного помещения;
- коммунальные расходы;
- заработная плата рабочих;
- рекламный бюджет.
Если речь идет о полноценном цехе, сумма первоначальных затрат на организацию производства составит не менее 3 млн. руб. При этом успех предприятия во многом будет зависеть от умения руководства наладить стабильный рынок сбыта газобетона. Для этого поиск потенциальных партнеров нужно начинать еще на этапе проектирования завода.